杨成鹏1, 冯炜森1, 林江嵘1, 郑茹悦1, 贾斐2 (1. 西北工业大学 力学与土木建筑学院, 陕西 西安 710072; 2. 西安电子科技大学 机电工程学院, 陕西 西安 710071)摘要:复合材料层压结构的单轴和多轴疲劳性能研究已在表征模型和方法等方面取得了显著进展。针对纤维增强复合材料层压板疲劳性能的分析预测,综述了疲劳损伤演化的曲线模型、剩余刚度模型、剩余强度模型、疲劳模量模型和S–N 曲线模型的研究进展,对疲劳失效判据和疲劳寿命预测的模型和方法进行了总结和分析,并就疲劳研究的不足进行了综合阐述。研究表明,疲劳损伤演化和寿命预测的理论模型多为宏观唯象模型,很少涉及微细观损伤形式和机理;针对多向层合板寿命预测的有限元方法虽然具有广泛适用性,但是还不足以模拟复合材料的真实损伤路径和历程。在此基础上,对后续复合材料疲劳损伤及寿命研究的重点方向进行了展望。 关键词:复合材料; 疲劳寿命; 损伤演化; 疲劳判据; 复杂应力 从上世纪60年代开始,碳纤维增强树脂基复合材料由于比强度高、比模量大、可设计性好等诸多优越性能被广泛应用于航空领域。发展至今,复合材料在航空结构中的应用已不限于非承力结构,而是有望大面积替代金属结构。与金属承力构件一样,复合材料承载件也存在结构疲劳问题,且疲劳损伤是引发结构失效的重要原因之一。因此,复合材料的抗疲劳性能已成为结构安全性和可靠性的重要指标,鉴于此,研究复合材料的疲劳性能具有重要的理论意义和工程价值。然而,复合材料的不均匀性、脆性、各向异性、损伤演变的复杂性、不同铺层间的耦合效应以及显著的层间应力,使得其疲劳性能的评估十分困难。 疲劳载荷的作用会严重影响复合材料层压板的基体、纤维-基体界面和层间结合性能。不同组分材料、不同铺层方式、不同载荷情况下复合材料的损伤机理不尽相同。试验表明,在低幅疲劳载荷作用下,复合材料的损伤机理与静载情况相似,可归纳为四种基本形式:基体开裂,纤维-基体界面脱粘,分层,纤维断裂[1]。不同模式的损伤萌生、扩展、耦合及相互促进,共同导致了材料刚度及强度性能的退化。在复合材料层压板的疲劳损伤过程中,大部分寿命阶段主要发生前三种形式的损伤,纤维断裂主要发生在层压板临近破坏之前较短的时间内。复合材料层压板的疲劳破坏过程可归结为损伤区(包括基体裂纹和分层)的扩展过程,特别是分层扩展过程[2]。疲劳损伤监测对揭示复合材料的疲劳损伤演化机理至关重要。Rosa等[3]应用红外热像仪监测了疲劳过程中复合材料的温度变化,并基于温度变化趋势提出了一种确定复合材料疲劳极限的新方法。莫淑华等[4]以电阻变化作为损伤参数,建立了复合材料累积损伤中电阻与疲劳损伤状态之间的关系,并对疲劳寿命进行了预报。程小全等[5]采用超声C扫描技术对复合材料疲劳损伤进行了有效监测。本文将对纤维增强复合材料在不同加载模式下的疲劳损伤-破坏形式和机理进行综合论述,并对用于疲劳损伤性能表征的损伤曲线模型、剩余刚度模型、剩余强度模型、疲劳模量模型和S-N曲线模型进行全面综述。同时,将对各类疲劳失效准则进行重点论述,并对复合材料疲劳寿命分析预测的模型和方法进行总结。
图1 单向复合材料的疲劳损伤演化过程[12] 



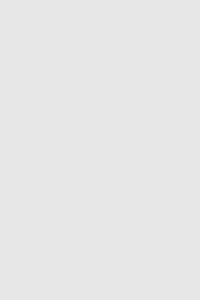
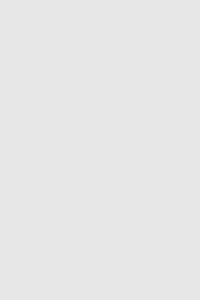
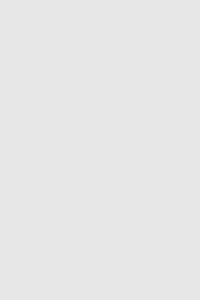
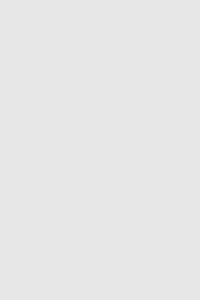
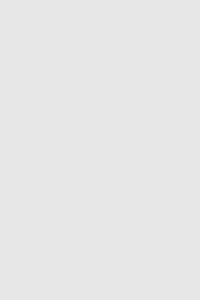
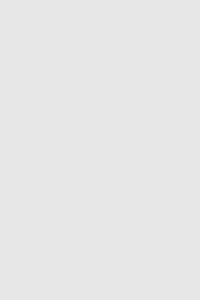
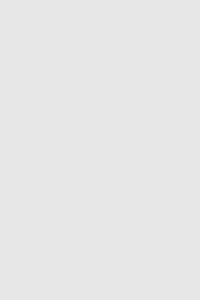
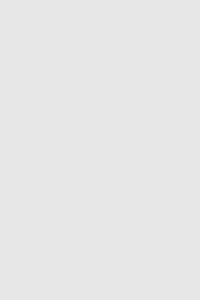
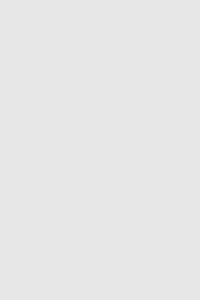
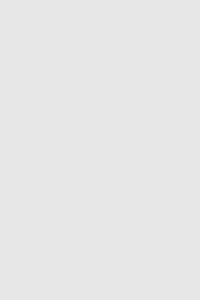
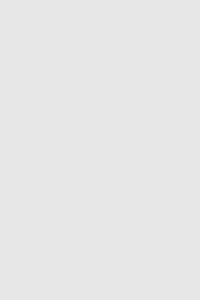
(a) GRP复合材料,ω=0.1 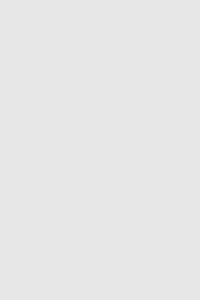
(b) GRP复合材料,S=48.5 MPa 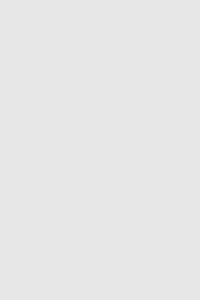
(c) GRP复合材料,S=63.6 MPa 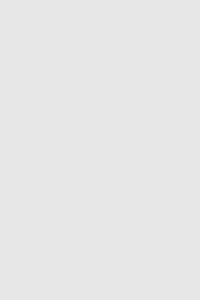
(d) GRP复合材料,S=78.3 MPa 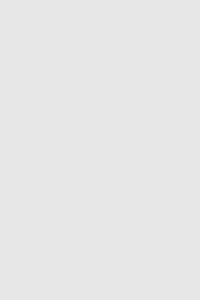
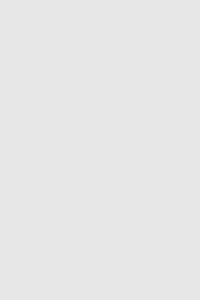
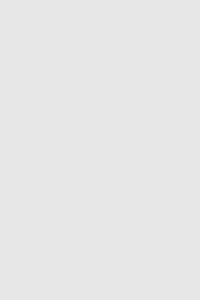
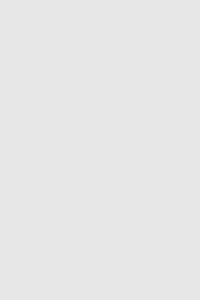
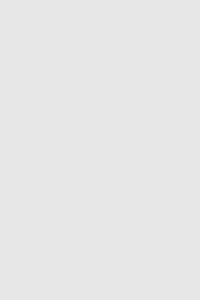
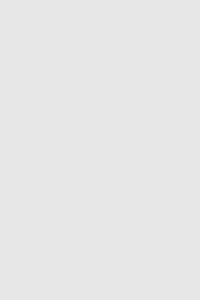
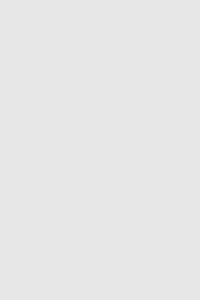
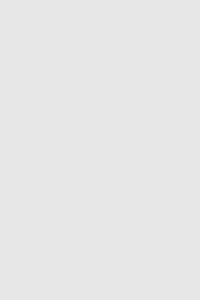
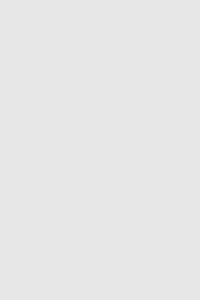
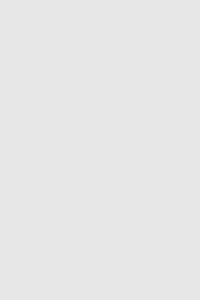
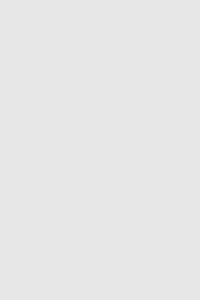
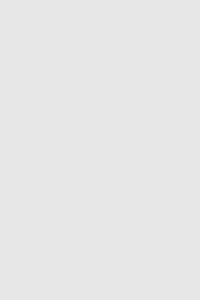
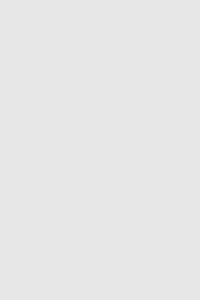
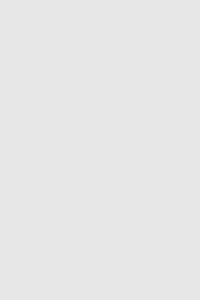
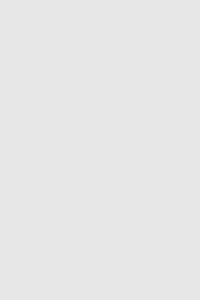
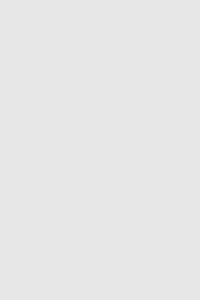
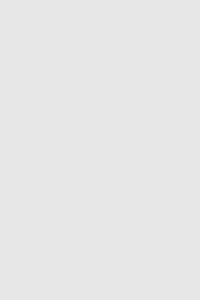
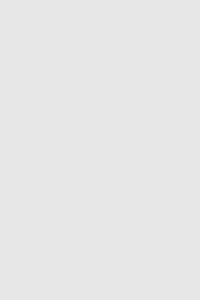
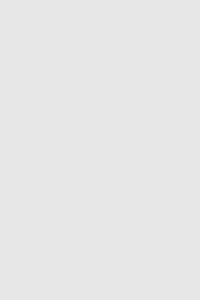
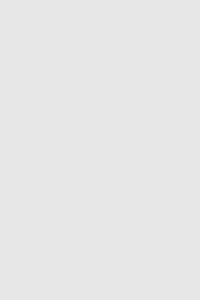
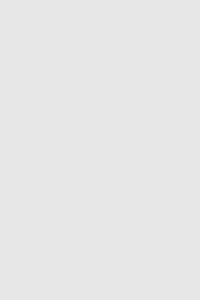
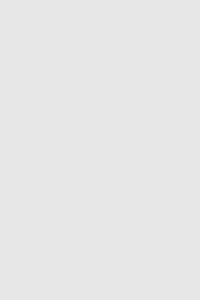
|