在浩渺的中国大地上,一座座超级轮胎工厂如璀璨的明珠镶嵌在工业版图上,这些工厂不仅具备强大的生产能力,更在技术创新和产品质量上追求卓越。它们拥有国际先进的生产设备和技术,通过自动化、智能化改造,实现了生产过程的数字化、网络化、智能化。同时,这些工厂还注重研发创新,不断推出新产品、新技术,以满足市场不断变化的需求。 今天,我们就来盘点一下,这些国内超级轮胎工厂。
2020年,中策橡胶投资近5亿元,打造高性能子午胎未来工厂。实现了全流程的智能化再造,大大提升了工厂效率,基本上6-7秒就可以生产一条轮胎。另外,中策在“未来工厂v1.0”基础上建设了第二座绿色5G数字工厂,也就是“未来工厂v2.0”。中策橡胶表示,该绿色5G数字工厂定位于生产中策旗下高端系列产品,包括高端旗舰系列、高端新能源专用轮胎EV PRO、高端配套、高端出口产品,以及自修复轮胎和静音棉轮胎等产品。正新集团正陆续在全球启动ESG推动工作。秉持着可持续发展的理念和服务,正新轮胎位于厦门的四个工厂——海燕厂、集美厂、漳州厂、实业厂,与福建华电集团合作的光伏发电并网项目正式启动运行,转换为光伏发电并网后,相比于普通发电,每年预计减少约8000吨污染排放。 【正新光伏发电并网项目】基于对绿色制造的坚持推进,厦门正新更是于2019年获得“国家级绿色工厂”认证,树立了行业典范。玛吉斯通过智能自动化改造,推动了工厂逐步从半自动化朝向全自动化生产转型。自2005年开始,玛吉斯投入12亿对工厂进行4.0智能化改造,全面导入工业4.0后的玛吉斯昆山工厂已经实现了“关灯生产”的自动化改造。据悉,该数字化工厂可以提升40%的生产效率。同时,工厂人员能精简25%,运营成本降低30%,产品研发周期缩短30%。 【机械手臂,替代劳力密集作业】针对轮胎制造智能化和信息化管理难度大的行业难题,赛轮集团打造了橡胶轮胎“智能制造示范工厂+橡链云工业互联网平台+行业最强产业链”,实现了智能工厂互联互通,提高生产效率,降低成本,推动工厂生产制造智能化、生产精益化。赛轮集团还搭建了全球首个“橡链云”平台,推动产业链数字化转型。玲珑轮胎打造了多个“智能工厂”,在国内已拥有招远、德州、柳州、荆门、吉林五个生产基地。玲珑轮胎各分公司通过MES系统,实现了实时采集产品生产设备所有的生产参数数据信息。充分利用海量生产数据完成智能制造中“自学习”“自决策”的关键数据的分析提取,为后期的各分公司之间的数据分析提供便利。另外研究并突破面向智能制造和工业互联网的共性关键技术,针对MES系统在生产作业方面的应用,重点研究异构设备实时数据采集数据与工业数据边缘计算以及制造大数据智能分析算法等关键技术。 图 生产现场米其林上海工厂以创新驱动,结合大数据和智能自动化技术,实现了从原材料、密炼、部件、成型、硫化、检测、入库的自动化的全流程智能化再造。 图为工人正在“标记”生胎 图为工厂智能仓储2021年和2022年,米其林上海工厂相继被评为“上海市绿色制造体系示范单位”“闵行区智能工厂”和“上海市智能工厂”。2023年米其林升级改造上海工厂打造轮胎智造“梦工厂”,并实施上海工厂二期扩建工程,提升产能的同时实现更高效、清洁且灵活的生产。德国马牌轮胎的合肥高新区工厂,是德国大陆集团在华投资的首家全外资轮胎生产基地,于2011年5月投产,该厂一期投资1.5亿欧元。
近日,德国马牌宣布,其合肥工厂四期扩建项目正式投产。预计在2027年满产后,合肥工厂的年产能将提高至每年1800万条乘用车和轻型卡车轮胎,目前,合肥生产基地的总投资额近10亿欧元。大陆马牌轮胎合肥工厂将采用先进的自动化技术,特别是在硫化区域将实现全自动化运输。这些新技术的运用保障了合肥工厂成为现代化、数字化,符合人体工学设计及可持续发展标准的工作场所。此外,合肥工厂大力投入创新环保设施,致力于将工厂打造为高能效的绿色工厂,到今年底,合肥工厂的太阳能年发电量将达到2700万千瓦时,可为目前的工厂生产运营提供18%的电力需求。近期,合肥工厂还获得了国际可持续性碳认证(ISCC) PLUS认证。兖州工厂是倍耐力在亚太地区的唯一生产基地,也是倍耐力在全球最先进的工厂之一,专注于高性能乘用车轮胎和摩托车轮胎的生产。倍耐力兖州工厂持续开展基于智能化和灵活性生产的数字化转型,以技术革新推进可持续发展理念。2020年,倍耐力兖州工厂入选国家级“绿色工厂”。2021年和2022年,倍耐力兖州工厂分别被当地政府评为重污染天气绩效评级A级企业。该工厂还凭借其在轮胎全生命周期中对可持续发展的严格要求,入选工业和信息化部公布的“第五批绿色制造名单”。重庆韩泰是韩泰轮胎在中国建设的第三家轮胎工厂,总投资9.5亿美元(约合人民币68亿元),主要生产乘用车胎和卡客车轮胎,年产能为1150万条。韩泰重庆轮胎厂自建设设计之初就一直倡导绿色发展理念,该轮胎厂还曾荣膺“国家级绿色工厂”称号。据悉,该工厂全面推进绿色低碳发展,实现了用地集约化、原料无害化、生产洁净化、废物资源化、能源低碳化。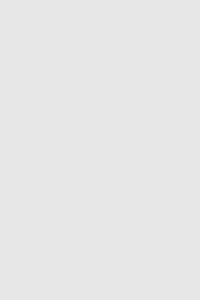 锦湖南京工厂是锦湖轮胎在中国的重要生产基地之一,该工厂均按照工业4.0的要求设计和建造,拥有先进的生产线和设备。从橡胶密炼、轮胎成型,到轮胎检验、仓库管理等整个生产流程,仅需很少人工干预,几乎都由智能机器设备完成。该工厂设有仓库管理系统、可编程控制器系统、射频识别系统、电气轨道系统等四大模块,可以确保生产、检测和物流智能化管理,提高制造效率。从2023年7月开始,锦湖南京工厂通过光伏发电部分供应工厂所需的电力,安装了3万多块光伏板,安装面积达81245平方米,预计每年可替代工厂所需电量的20%以上。另外,锦湖南京工厂还获得了“2019年度南京市智能制造工厂”认定和“2023年度江苏省智能制造示范工厂”认定。万力轮胎作为广州工控属下一家大型国有企业,其从化生产基地于2005年投产,全线引进节能、低耗、自动化的先进生产设备,采用行业领先的生产工艺,致力于生产绿色高性能子午线轮胎;合肥工业4.0生产基地于2016年正式投产,标志着全国首个全领域智能化、全流程自动化、全方位绿色化的轮胎从构想成为现实,从原材料入库至成品出库,全过程“自动化、信息化、智能化”。近年来,万力轮胎以智能制造创新引领行业进步,今年1月,万力轮胎三期工程年产1200万条轮胎项目开工仪式在从化基地举行。在三期项目前,万力从化基地已具备每年生产2400万条半钢子午线轮胎的能力,为国内产能最大的半钢子午线轮胎单体工厂之一,能耗优于行业先进值。作为中国轮胎行业“新智造”的代表,浦林成山多年来持续践行“绿色化、智能化”发展战略,打造以绿色标准、绿色工厂、绿色产品、绿色厂区为核心的绿色先进制造体系。 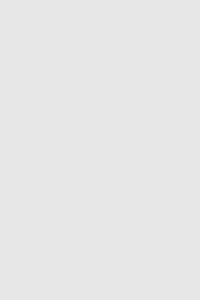
目前中国、泰国两大绿色智能生产基地,已全面实现能源管控网络化、能源利用低碳化、轮胎生产洁净化和原材料无害化。2023年浦林成山山东生产基地获评工信部“国家级绿色工厂”;泰国生产基地建成泰国目前最大工厂屋顶光伏发电项目;企业连续第八年蝉联石油化工“能效领跑者”。 山东生产基地产能优化项目、泰国基地半钢子午线轮胎三期扩产项目目前已全面启动。2023年,浦林成山投资1.4亿元,对半钢1000万套生产线进行物流智能化改造。 另外,浦林成山与国内知名橡塑机械厂合作开发特制串联式密炼机,生产效率提高51%,能耗降低10-15%。在智能物流方面浦林成山通过射频识别技术,从炼胶RFID识别-半成品投料识别-载具绑定RFID-物料条码及自动打印数贴-最后设备的RFID识别,物料数字化防错,从而实现智能化的管理。 2021年2月,贵州轮胎、联通、华为三家企业合作搭建“5G全连接工厂”项目完成验收,这也是轮胎制造行业首个“5G全连接工厂”。贵州轮胎的5G先进轮胎工厂充分利用智能制造技术,实现了生产全过程的高度自动化、数字化。从轮胎成型到检测,每一个环节都借助机器人和自动化装置,大大提高了制造效率和产品质量。换句话说,工厂实现5G网络全覆盖,每一个环节、每一个产品的生产数据都实时收集到智能生产MES系统,让上下游各个环节联结协作更紧密,极大地提高了生产效率。由于该工厂“智能化、数字化”程度极高,贵州轮胎5G智能制造工厂还曾被评为“贵州省数字化智能化融合升级标杆企业”。和之前相比,现在的贵州轮胎工厂产量提升了46%,人均产出效率提升57.1%。前不久,“贵州轮胎5G先进轮胎制造工厂”还获得央视《新闻联播》与《焦点访谈》两档节目的报道。通用股份半钢智能工厂是通用股份积极践行工业4.0战略、在行业内率先打造的“黑灯工厂”。在这里,大数据、云计算、人工智能等先进技术得到广泛应用,机械手臂、EMS小车、堆垛机、全自动硫化机等智能化设备成为生产主力军,共同构建轮胎制造全生命周期的数据平台,实现“人效、品效、能效”的三大提升,取得生产效率提升40%、运营成本降低20%的显著成效,并荣获“江苏省示范智能车间”荣誉称号。双星“工业4.0”智能化工厂打破了传统轮胎企业的生产工艺和集中式的生产方式,集成全球最先进的信息通讯技术、数字控制技术和智能装备技术,融“产品定制化、企业互联化、制造智能化”于一体,搭建了一个由用户(订单)指挥、数据驱动、软件运行的智能生态系统。在ESG体系建设方面,双星始终将社会责任与企业高质量发展相结合,从轮胎研发、制造、服务到废旧轮胎循环利用,全面对标ESG标准,打造全产业链和全寿命周期的绿色化管理,实现可持续发展。2014年森麒麟在山东青岛建立了中国首家轮胎工业4.0智慧工厂,整条生产线依托大量智能化设备,实现了从原材料、密炼、部件、成型、硫化、检测到入库的自动化、信息化和智能化生产。相比传统生产线用地面积降低50%,单台设备产出率提升50%,产品合格率达到99.8%。森麒麟自主研发的“智能制造系统”相较于传统生产线工厂生产效率提升约20%,设备利用率提高约15%,同时降低了设备维护成本、采购成本和库存成本。华盛橡胶建设了MES、ERP、WMS信息化系统,全方位收集车间生产的数据信息、进行生产流程全过程管理。同时,优化工艺配方参数及工厂网络布局等,主要生产设备大量配备PLC、传感器、伺服电机等,并配套工控系统,实现设备的自动化控制。华盛橡胶升级数字化车间后,生产效率提升15%,能耗降低8%,用工人数减少28%,产品合格率由99.85%提升至99.98%,故障排查时间缩短40%,产能利用率在96%以上,库存积压下降10%,产品入库、发货错误率降低至0。雄鹰轮胎2021年启动数字化体系建设项目,雄鹰青州工厂已实现全流程数字化智能制造系统的贯通,全工序智能目视化管理,一举建成智能制造数字孪生工厂,并荣获“2023年度中国智能制造最佳应用实践奖”。雄鹰轮胎在数字孪生工厂的建设过程中展现出了卓越的实力。通过搭建数据中心、组建各级网络、搭建网络和数据安全体系,确保了生产数据和检测图像的集中安全保存。同时,企业全力打造数转制改项目,建立智慧制造创新中心,增上综合安防管理平台,智慧园区一卡通系统和研发项目管理系统,不断加快企业数字转型步伐。永盛橡胶智能工厂自2023年4月开工建设,总投资约7.8亿元,引进了国内外先进工艺及生产设备,嵌入智能化生产软件系统,从原材料入库到产品出库进行全流程智能化改造升级。永盛橡胶半钢总工程师张传辉表示,“我们要建设的工厂不是传统的光纤、无线WiFi这种模式,而是5G全连接,将数字信息化作为核心,我们在智能仓储、智能物流和技术方面的投资,达到5亿元”,该项目采用的5G物联网系统,技术水平已属国内领先水平。今年3月26日,永盛橡胶智能工厂高性能轮胎首胎下线。永盛橡胶设备处处长王文正表示,该智能工厂预计今年10月份全部达到投产运营状态,日产能16000条轮胎。看了上述内容,你认为哪些是中国超级轮胎工厂?欢迎投票留言。
|