当下冲压车间生产管理现状
冲压车间生产管理系统,主要管理冲压车间的生产实绩、返修报废、库存管理。
冲压车间目前已有系统管控了成品入库、成品出库、成品库存;可统计查询车间的成品库存情况,进行库存盘点,返修出库、返修入库,不良品统计。生产完工后打印条码,挂在容器上,入库进行批次管理。与生产现场大屏接口,显示内容主要是计划、实际,内容为手工录入。
冲压车间管理所需要的各种报表格式变化频率较大,不能满足现有管理的需要。

冲压车间生产管理目标
通过冲压生产系统,实现卷料、板料的入库生产管理;冲压件入库、生产和返修管理;卷料、板料、冲压件的在库管理查询;零件履历表的生成和查询;管理表格生成、打印;板料、冲压件在仓库转存管理。
冲压车间生产管理功能描述
计划调度管理
根据上层系统给出的计划,制造工艺路线,对产品的生产进行每个工序工位的详细调度,通过有限资源能力的作业排序和调整来优化车间性能。其中包括对产品定义工艺路线,根据工单、序列号进行跟踪指导。
生产实绩管理
获取生产线的产量数据,停线时间,产品的一次合格率等生产效率和生产决策要素,通过对整车生产各个管理点的信息采集管理,通过条形码和电子数据交换技术取得生产通过的各项信息。
将实际制造过程测定的结果与过去的历史记录和企业制定的目标以及客户的要求进行比较,以报告或在线显示的方式输出,用以辅助业绩的改进和提高,通过系统自动计算的形式对生产实绩进行管理 。
冲压车间目前已有系统管控了成品入库、成品出库两个生产实绩采集点,未来增加系统管理范围,从卷料入库到冲压件出库,新增卷料入库、板料入库、板料出库3个生产现场的控制点,以便记录中间件的生产、在制情况。提供卷料、板料、产成品的在库管理台帐。
生产增加更详细的批次管理,从卷料入库到冲压件出库的批次管理,便于追溯;同时对于返修、报废进行系统内管理,提供返修出库、返修入库、报废等功能操作,利于车间产成品库存的状态转换。
生产指示管理
资源监控:在生产执行过程中,不管是人还是机器设备,包括工具、物料的如何协调配合进行生产,都需要系统来进行指示操作,而且系统需要跟踪每个产品、重点工序现在的工作状态和刚刚完工情况。
状态监控:监测到产品的适时状态,工序的生产情况,关联设备、生产线运转的适时情况如何,对设备运行情况的掌握,对生产设备的适时监控,对设备可动率的分析,对生产性、计划/实际差异分析。
结合计划调度管理和生产实绩管理,通过与生产现场大屏直接接口,生产现场大屏除显示生产计划、生产实际;对生产现场进行指导,换零件生产时,进行大屏提示;
统计过程控制
在实际生产中,经常会要求对某个工段、某个时刻、某个期间的在制品、零件消耗、下线产量的统计,通常在物理点上以关键工位和特殊的环状工序为为分界点,通过统计过程控制,能够为预测车辆的预定交货期提供可靠的数据支撑。
通过生产实绩管理,对于半成品、成品的生产、在制情况进行统计,同时反过来对于后期的计划编排提供数据支撑,以便更合理的安排生产。
设备维护管理
对数控机床、轨道托盘、旋杯、工控设备的状态进行生产监控,并同时进行数据收集和维护指导等相关措施。
根据监控、收集的数据,对机器设备进行有针对性的维护,保证机器设备和相关资产的正常运转,以实现企业的相关目标要求。
冲压车间的设备是24小时不间断工作,通过在换模时采集更换模具时间、设备停机时间等信息,了解设备的使用率,更好的支持设备维护。
全程质量管理
通过监视工位、工件在任意时刻的位置和状态、扭矩等测量参数的记录来采集每一个产品的历史,该记录向用户提供零件或总成的批次及每个最终产品使用情况的可追溯性。
应当遵循生产过程中的工艺标准的执行,对质量标准的严格控制,对产品缺陷追踪,满足质量保证体系、顾客交货期保证,当商品车发生质量缺陷时,系统应该能够提供批次甚至精确产品的数据。
对于冲压加工中的不良品,提供返修管理,并统计不良品的返修成功和报废情况。
人力资源管理
指导:提供按分钟级更新的员工状态信息数据(工时,出勤等),根据人员资历,工作模式,业务需求的变化来指导人员的工作。
跟踪:对工序工时、生产效率KPI的追踪,能够省去人工报表,以分钟为单位提供每个人的状态,再根据时间效率的对比,结合出勤报告,效率跟踪,及行为规范,包含成本及工具准备作业,等这样的间接的行为跟踪人力能力。主要记录班次的上下班,可以跟踪到产成品生产时的班次信息。
冲压车间生产管理小结
以上通过对冲压车间的生产和管理现状的分析,结合冲压车间生产的信息化目标,总结了冲压车间生产管理的核心功能,主要包括:计划调度管理、生产实绩管理、生产指示管理、统计过程控制、设备维护管理、全程质量管理、人力资源管理七大方面。其中,计划调度是先锋,一切生产均以计划执行,在实际的生产过程中,包含了生产实绩的采集,以及生产指示的展现,通过生产过程中的生产实绩的数据采集和设备数据的收集,可以生成各种统计报表,也是质量管理的数据来源;人力资源管理是冲压车间管理的辅助管理功能。
总之,通过以上八个方面的功能,涵盖了从计划到执行,以及计划的调整反馈整个生产过程管理的方方面面,不论是成熟产品的选型还是自主开发,只要覆盖了这八大方面的功能,再与现有系统进行良好的无缝集成,定可以实现该厂冲压车间的生产管理系统化,减少各种生产数据的人工录入以及统计,保证了生产数据的实时和真实性,真正提高冲压车间的生产效率。

二、关于冲压生产运行管理与效率提升主要思路
业内衡量综合生产运行效率的指标为:设备综合效率(Overall Equipment Effectiveness),其计算公式如下:OEE=可用率×表现性×质量指数。其中:可用率=操作时间/计划工作时间;表现性=总产量/(操作时间/理想加工一单位产品的周期时间)=总产量/(操作时间×理想生产速率);质量指数=良品/总产量。利用OEE的一个最重要目的就是减少一般制造业所存在的六大损失(停机损失、换装调试损失、暂停机损失、减速损失、启动过程次品损失和生产正常运行时产生的次品损失)。图1是六大损失的说明及其与OEE的关系。本文以某公司冲压车间为例,从降低以下两个损失着手,提升效率:⑴换装调试损失。通过优化切换过程和生产计划安排,降低切换过程的绝对时间损失和相对时间占比,提高“有效率”;⑵减速损失。通过开展SPM(Stroke Per Minute)目标设定和管理工作,逐步提高“表现性”,同时设定ASPM(Actual Stroke Per Minute)目标,应用TIP工具分析问题,提升运行稳定性。
图1 六大损失与OEE的关系
绝对切换时间分为两部分:模具切换和板料切换。目前板料切换依靠双工作台和定位刻度线固化设置,基本可以在机外完成准备工作,并不停线完成切换,故在此重点讨论如何降低模具切换的停线时间。目前大多数车企均采用全自动整线换模方式进行切换,其过程速度受硬件设备、自动化技术和程序优化等多方面影响,实际表现各有不同。表1 2016年1月至10月平均单次模具切换停线时间

从表1可以发现,10月平均单次9.20min的损失时间明显过多,其一是与冲压多品种,小批量生产的频繁变化有关,其二是切换过程尚有多处可以优化提升之处。为降低切换损失,通过分解模具停线切换过程的设备和人员所有动作内容,得出如图2所示的模具自动切换流程图。分析压力机自动切换逻辑,发现图中红色字体步骤动作时,压力机滑块处于静止状态,重力势能相对稳定,过程时间约2min。经过研讨,实施“单台压力机光栅”代替“整线安全门联锁”机构的能量锁定功能,实现了人工更换端拾器工作与设备动作的并行,在实际应用中规范标准化作业,解决问题点和瓶颈点,将切换过程工作梳理明确,使得整体切换损失大大降低。表2是以实际运行的真实数据为基础,单批次生产600冲次,SPM为10冲次/分钟时,模具切换时间占比将由10月的13.3%下降至12月的11.2%,直接为“有效率”的提高贡献2.1个百分点。
图2 模具自动切换流程图
表2 2016年10月至12月平均单次模具切换时间

前面讲到降低模具切换的停线时间对“有效率”提升的贡献,同时也带出了切换时间占比的概念:切换时间占比=切换停线时间÷(切换停线时间+故障停线时间+生产冲次批量÷SPM节拍目标)×100%。在理论计算时,将故障停线时间设置为0,则切换时间占比=(SPM节拍目标×切换停线时间÷(切换停线时间×SPM节拍目标+生产冲次批量))×100%,由此可知,公式中三个要素对占比的影响是:生产冲次批量越高,切换时间占比越低。可以看到,SPM节拍目标的降低和生产冲次批量的提高与“多品种,小批量”生产模式下的精益生产是背道而驰的。因此,除了不断降低绝对的模具切换时间外,如何合理管控生产批量,最大限度利用库存资源,保持生产运行的稳定高效才是关键。冲压生产的库存成本主要集中在自制件库存,一般采用PFEP(单一零件物流需求)清单和MIN/MAX库存控制工具管理,而生产批量在很大程度上都是由自制件的MIN/MAX决定的,故库存与生产批量必须整体分析和管控。为实现库存的动态管理和持续优化,我们按以下的思路回顾PFEP和MIN/MAX:
图3 客户需求
①每月下旬核算已锁定的客户需求(下游车间上线计划),分析各自制件需求量和交货时间要求,如图3所示。Layout布局设置,定义需要做出调整的自制件的PFEP和MIN/MAX值,图4为库房Layout。
图4 库房Layout
库位设定过程需结合需求量,考虑冲压生产时的入库物流和配送过程的路程,尽量的减少距离,同时需考虑尽量减少入库和配送过程的作业干涉,保证物流顺畅;MIN/MAX值设定需在充分考虑下月锁定和后续预测需求的前提下,提高库房面积的利用率。理想关系式:生产批量=MAX-MIN=供货周期内需求零件数量。在这种状态下,库存都将成为有效库存,可以很好的进行管理和预警应用。如前所述,实际冲压运行时,MIN/MAX的设定不仅考虑了生产批量的满足,同时还最大限度的利用了库存场地和工具料架资源,预测了后续客户的需求变化,往往MAX-MIN大于生产批量。实际运行中的关系式一般会处于这个状态:生产批量≈供货周期内需求零件数量≤MAX-MIN。
因生产批量的底线由准备时间决定,准备时间=外部模具/板料准备时间+模具切换停线时间。越快的准备能力与切换速度,就越能够提升我们应对“多品种,小批量”生产模式和市场需求的变化。生产批量目标见表3。表3 生产批量目标

减速损失
冲压行业的产能指标一般使用SPM或SPH核算,其中SPM适用于更高节拍的冲压生产线的日常管理,而冲压产能一般满足如下关系式:设备最大产能≥设计目标产能≥实际产能输出,而实际产能输出与设计目标产能的差距,就是减速损失,为此实际运行的SPM管理与提升成为降低减速损失的关键。在采用机械手和整线连续自动化模式的冲压生产中,SPM提升的瓶颈或难点主要在以下几个方面:1)产品和模具设计状态。产品的尺寸、形状、重量等因素越是偏大或复杂,SPM的上限相应偏低,而模具结构、工法布置等复杂因素会大大影响机械手运动轨迹的调试和优化,从而限制SPM提升,而此点在设计时会进行CAE分析,明确设计极限。2)产品的质量状态。良好的质量输出是制造业的根本,所有的产品都有自己独特的质量特点,良好而稳定的质量状态是提升SPM的前提。3)物料准备与物流周转。冲压生产中有多种物料、工装的物流形式,它们都是生产稳定高效运行的必备条件,所谓牵一发而动全身,SPM的提升,同时也是提高了对它们的响应要求。因此,我们建立了SPM目标管理与提升的制度规范,其中清晰定义的产品由首次上机调试开始到SOP后常规生产过程的SPM建立和管理流程,同时使用工艺纪律审核检查执行效果,分析目标运行状态和问题,寻找改进点。图5为冲压车间节拍变更计划。减速损失是指所有影响产能目标达成的问题,除了SPM的管理和提升,生产过程的启动和停止过程造成的实际输出速度的降低也是提升点。表4为ASPM和SPM目标对比表。ASPM目标的粗略范围一般控制在近期实际ASPM的平均值与峰值之间,结合冲压生产整体产能/效率目标和各产品线的特殊性,通过讨论达成一致。图6为TIP对ASPM目标达成的分析图。
图5 冲压车间节拍变更计划
表4 ASPM与SPM目标对比表
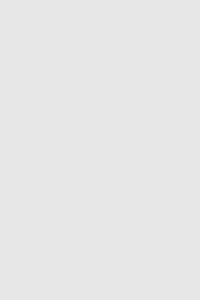
应用改进效果总结
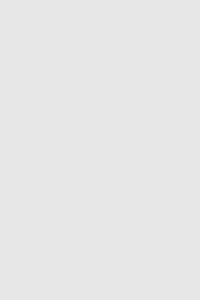
图6 TIP对ASPM目标达成的分析
通过以上多方面工具的应用和改进,不仅生产组织更加合理有序、管控到位、资源利用充分,产品满足能力大大提高,而且在OEE(设备综合效率)表现上取得了明显的提升。改进前9月份的数据(常规产品)为:有效率=77.8%,表现性=9.75÷10×100%=97.5%,质量指数=98.6%,OEE=74.79%。改进完成后12月份的数据(常规产品)为:有效率=85%,表现性=9.875÷10×100% = 98.75%,质量指数=99.46%,OEE=83.48%。因为非常规产品(订单车型等)需求量过少,其OEE是要远远低于常规产品的,整体测算的OEE大致在80%左右,应该说综合效率的提升是显著的。结束语
精益生产的基本方法是拉动式生产,即根据客户需要的产品和数量实时安排生产,因此其长远的目标是“零库存”生产。现在的“多品种,小批量”在今后必将变成更多品种、更小批量、更频繁的变化和更短的交货周期,这一切都要求我们必须不断优化运行管理体系,提高维护保养水平、响应速度,随着这些能力的逐步提升,我们才能够逐步降低自己的库存,直至维持“零库存”状态,才有可能向智能化生产迈进。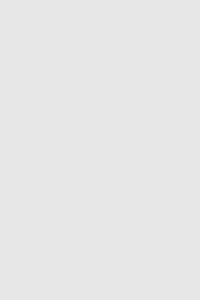