☞ 这是金属加工(mw1950pub)发布的第19984篇文章
越来越复杂的液压作动筒类零件的细小深孔加工,主要存在断屑、排屑和冷却的加工难题,通过在车铣复合机床应用机械式振动钻孔技术,选用合适的深孔加工刀具,结合合理的切削参数,解决了大长径比的深孔加工难题,实现了大长径比油管孔在车铣复合机床的高效加工。
在钻孔加工工艺中,“长径比”指被加工孔的深度与直径之比(即L/D),一般长径比>10的孔被称为“深孔”[1]。随着零件的复杂性、整体性等越来越高,深孔加工越来越普遍,钻削技术也被广
泛应用。深孔麻花钻、枪钻、BTA钻、喷吸钻以及DF钻等钻削刀具的出现[2],结合新型的机械振动钻孔、超声振动钻孔、液压振动钻孔和电磁振动钻孔等深孔加工技术的应用[3],使得深孔加工能力较之以往有了很大的提升。但深孔加工由于其特殊性,钻头进入工件时是在半封闭条件下工作,在实际加工时受到较多限制,不能直接观察到刀具切削情况[4];切削热不易传散,必须采用强制有效的冷却方式;排屑困难;钻杆需要足够的刚性等。这些难题使得其实际应用效果差异较大,还需结合零件实际加工情况进行验证、总结。
某典型液压作动筒筒体零件局部结构如图1所示,该零件材料为30CrMnSiA,热处理后硬度为35~41HRC,其集中了复杂的外形铣削、深孔镗削和精密孔系的加工,还包含有3组 、长径比最大达63的油管孔加工,有效深度分别为L1=559mm、L2=347mm、L3=282mm(下文分别称为 “559”孔、“347”孔、“282”孔、),孔的直线度要求在100mm长度上偏移量≤0.2mm,表面粗糙度值Ra=3.2μm。
 图1 某筒体零件局部结构示意 这类深孔传统的加工方式选择专用机床,每加工1件零件的3组油管孔就必须更换3套专用夹具,采用的专用机床及专用夹具如图2所示。
 a)专用机床 b)专用夹具 图2 专用机床及专用夹具示意
完成该零件3处深孔加工内容,单件纯切削时间需要6.58h,切削时间统计见表1。 表1 某零件在专用机床加工深孔的单件切削时间 (单位:min)
从表1中可以看出,采用专用机床加工效率低下,加工周期繁琐冗长。针对批产零件来说,该深孔工序成为加工瓶颈,急需在加工方法、加工效率上有所改进,才能满足生产需求。
3.1 深孔加工的难点
深孔加工主要存在以下难点。
1)长径比大:L/D>10的深孔在加工过程中,不易观察导致无法判断刀具状态,不易测量导致难以保证精度。
2)排屑难:切屑不易排出,切屑经过的路径
长,容易发生堵塞,造成刀具崩刃,很容易划伤加工表面,影响表面质量。
3)散热差:切削热不易传散,刃口容易过热导致刀具加剧磨损。难加工材料如钛合金、高温合金等增大加工难度。
4)刚性差:过长的钻杆刚性差,易变形,易振动,孔易偏斜[5]。针对深孔加工过程中的难题,可以从冷却润滑、排屑、合理导向及断屑处理等几个方面采取有效措施。高压内冷可以起到冷却润滑并排出切屑的目的,最好选用油基切削液;采用导向块或者提高引导孔精度的方法可以提高导向的正确性;采用自激振动、强迫振动的方法或者增加刀具断屑槽的方法可以快速断屑,利于切屑的排出。
3.2 车铣复合机床的功能
先进高端数控机床的应用,使得加工内容越来越集中。车铣复合机床的结构如图3所示,其中M1=3、M1=4分别代表车削主轴S1正转、反转,M3=3、M3=4分别代表铣削主轴S3正转、反转。车铣复合机床的应用,使得车、铣、钻、镗、铰、齿
加工、深孔加工和偏心加工等可以集中到一道工序来完成。这样就会使加工工艺更加灵活,工序更加集中,不仅提升了工艺的有效性,还减少了零件在整个加工过程中的装夹次数,使加工的精度更易获得保证。特别是其具有的深孔加工能力,在液压作动筒筒体、活塞类零件加工时,优势特别明显。本文中选用的WFL车铣复合机床具有80bar(最大350bar,1bar=0.1MPa)的高压内冷功能,加上其具有的深镗燕尾单元,可以高效地完成深孔加工。
 图3 车铣复合机床结构示意
3.3 枪钻刀具
深孔加工刀具有深孔麻花钻、枪钻、BTA钻、喷吸钻和DF钻等刀具,结合零件加工特征及孔径大小、刀具成本等综合因素,针对该零件的加工,选择φ9.13mm钎焊式枪钻。枪钻属于外排屑式深孔钻,如图4所示。其主要用来加工直径为3~30mm的深孔,长径比可达100,加工孔的精度为IT8~IT10,加工表面粗糙度值Ra可达0.8~3.2μm。
 图4 枪钻示意
枪钻的几何角度如图5所示。钻尖的位置与旋转中心不重合,切削过程是沿着相交于钻尖的内外切削刃进行的。枪钻的刃磨几何角度对于其断屑及寿命有很大影响。
 图5 枪钻几何角度示意 3.4 机械振动钻孔技术
(1)振动钻孔原理 振动钻孔,即在钻孔的过
程中叠加有振动的动作过程[6]。按照振动钻孔的性质可以分为自激振动钻削和强迫振动钻削;按照振动的装置可分为超声波振动、电磁振动、液压振动和机械振动[7]。本文选择法国MITIS的机械振动钻孔技术来解决车铣复合深孔加工刀具寿命过低、加工质量不稳定的问题。机械振动刀柄是利用电动机驱动偏心凸轮旋转产生振动的装置,如图6所示。机械振动辅助制孔技术通过在恒定的进给运动基础上,叠加正弦往复运动,形成“微振动进给”[8],从而产生周期性切削,为散热及断屑提供了较好的条件。
 图6 机械振动刀柄
(2)振动钻削影响因素 振幅及切削参数的调整对断屑影响很大。振动钻削的3个主要参数有:振幅、频率和进给量。振幅、频率和进给量对于实际钻削角度、实际切屑长度和钻削扭矩都有极大影响。
(3)振动钻削的特点及优势 主要特点及优势如下。
1)提高加工精度和表面质量。采用振动钻削的孔壁表面光滑均匀,不产生积屑瘤。普通切削过程中易存在积屑瘤并参与切削,将使切削刃径向尺寸增大,造成扩切的影响。振动钻削则破坏了积屑瘤存在的条件,正好完全消除了因积屑瘤引起的孔径扩大。
2)可减小钻削力和钻削扭矩。振动切削是一种运动速度和方向不断变化的脉冲切削,有助于金属趋向脆性状态,塑性变形减少,摩擦系数降低,从而不仅减小钻削力和钻削扭矩,也可减少功耗。
3)切削温度明显降低。传统钻削是一种半封闭式切削,钻孔时产生大量的切削热[9]。工件和钻头易由于孔内散热不及时而导致热膨胀变形,直接使得孔径扩大。振动钻削则因其轴向力和扭矩较小,且冷却润滑更加充分,故切削温度大幅度降低,对孔径的扩大起到积极的遏制作用。
4)切屑处理容易。钻削加工中的排屑状况直接影响到孔径扩大程度。若在钻削过程中排屑不畅,不可避免地产生切屑参与切削中的挤压和摩擦的问题,从而使孔径扩大。振动钻削具有良好的断屑和排屑能力,使因切屑堵塞而引起的孔径扩大问题得到了根本性的解决。
5)减少刀具磨损,延长刀具寿命。振动切削除了具有由于钻削阻力减少和钻削温度降低的综合作用而使刀具磨损减少、寿命延长的作用之外,更加深层的因素是轴向振动钻削的振动作用使得振动钻头具有刚性化效果。即在钻削过程中由于施加脉冲式的切削力,钻头的刚度得到显著地提高,所以钻孔时钻头更不容易弯曲变形,有效地延长刀具的使用寿命[10]。 4.1 车铣复合深孔钻削工艺流程
在车铣复合机床钻削深孔,跟传统的专业深孔钻床的加工工艺不同。专业深孔钻床加工深孔,需要专用夹具,专用夹具上的钻套,直接保证了孔的位置及精度。而在车铣复合机床上钻削深孔,无需夹具,也不用钻套。由于加长麻花钻或者枪钻自身
的重力,以及刀具的长径比,使得对于深孔来说无法定位孔的位置,所以只能通过钻削引导孔来确保位置及精度。加工工艺流程如图7所示。
 图7 车铣复合深孔钻削工艺流程 主要流程为:①钻引导孔,引导孔直径大于枪钻直径0.01~0.02mm(IT7),深度最小2.5D。②低
转速(≤30r/mi n)、低进给且反转进入,在离引导孔有效深度1~2mm处暂停,开启切削液。③提升转速至正常切削速度,开启进给运动进行钻削,刀具不能回退,多观察切屑形态。④钻至有效深度后,枪钻在孔底快速回退至引钻处,停止转动与冷却,快速回退至安全位置。
4.2 机械振动钻孔加工过程
基于机械振动钻孔的加工优势,借助机械振动刀柄配合枪钻,通过在刀具直线进给运动的基础上,叠加正弦往复运动,形成“微振动进给”,起到断屑的目的,从而提高加工质量和延长刀具寿命。
(1)刀具的装夹 采用机械振动钻孔技术,选用法国MITIS振动刀柄装夹枪钻,如图8所示。由于其刀柄结构为ER32卡簧接口,所以必须使用密封圈,来保证内冷压力不泄压。
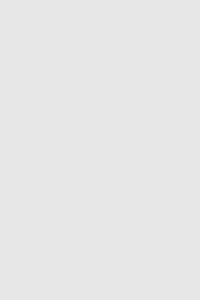 图8 MITIS振动刀柄装夹枪钻示意(2)加工程序 按照车铣复合枪钻的加工工艺,先钻引导孔,镗削引导孔,再用枪钻直接加工到有效深度,程序编制如下。
N1; (DRLL D9.1 HOLE) CDS
TLCH1(“ZT9D1”,-90) TLPREP1(“XTD9D15”) MCMILLS1 MCUTLIM(15)G54 G64 G95 S3=2500 M3=3 F0.06 G0 X1=59 Y1=-16 Z1=150 C1=0 M3=7 DRILL(0,20,3,20) G0 Z1=150 CDS M00
N2;(BORING D9.15 HOLE) CDS TLCH1(“XTD9D15”,-90) TLPREP1(“QZ9D13”) MCMILLS1 MCUTLIM(10) G54 G64 G95 S3=1200 M3=3 F0.05 G0 X1=59 Y1=-16 Z1=150 C1=0 M3=7 DRTURN(0,20,3,19.8,0,0.05) G0 Z1=150 CDS M00 N3; (DRLL D9.13 HOLE) CDS DK M00 TLCH1H(“QZ9D13”,-90) TLPREP1(“”) MCMILLS1 MCUTLIM(10) G54 G64 G95 S3=50 M3=4 F0.06 G0 Z1=20 C1=0 G0 X1=59 Y1=-16 Z1=5 G1 Z1=-1F1 M00 G1 Z1=-15 F0.5 M3=5 M99 S3=1400 M3=3 G4 F2 Z1=-560.5 F0.015 G4 F2 S3=300 G0 Z1=-15 M3=9 G0 Z1=10 X1=200 M00 TLCH1H M30
(3)加工试验参数 使用机械振动钻孔技术,加工参数增加了振幅和频率。根据零件材料特性、热处理状态、装夹刚性和刀具材料等验证不同切削参数、不同振幅加工时的断屑情况,控制切屑形状、提高加工质量和刀具耐磨度。振幅和频率、进
给量对于刀具的磨损程度及断屑情况影响较大,具体试验参数见表2。 表2 振幅、切削参数对加工质量及刀具的影响
(4)加工试验结论 主要结论如下。
1)使用机械振动钻孔技术断屑效果好,切屑的长度基本在3~7mm;不使用机械振动钻孔技术加工,切屑的长度基本在18~35mm。两种加工方式下切屑长度对比如图9所示。
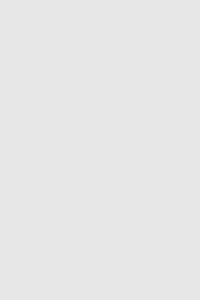 a)使用振动钻孔技术
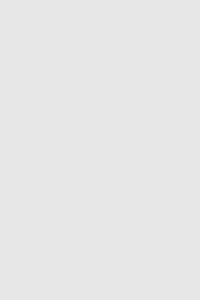 b)不使用振动钻孔技术 图9 切屑长度对比
2)振幅的大小与切削参数匹配的合理性,直接决定了不同切屑形状的产生。在深孔加工中,判断断屑及排屑顺畅的标准是在加工过程中能否产生C形屑,C形屑的产生对于内孔表面粗糙度及刀具寿命也有一定好处。
3)机械振动钻孔对刀具寿命也有很大影响,与常规钻孔方式相比,刀具寿命有明显提升。从切削统计数据来看,加工同样深度的孔,使用机械振动钻孔技术后,刀具寿命相对于使用侧固刀柄寿命提高30%以上。图10为相同加工条件下的刀具磨损情况对比。
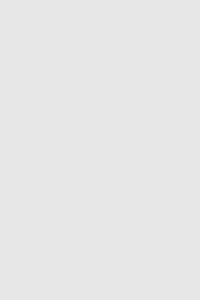 a)使用振动钻孔技术 b)不使用振动钻孔技术 图10 刀具磨损情况对比
4)加工质量与加工效率。使用机械振动刀柄振动钻孔后,断屑与排屑效果明显优于侧固式刀柄。从验证的多批次零件的数据来看,零件的加工质量较好,特别是孔的直线度在100mm长度上偏移量都在0.12mm以内,杜绝了枪钻在零件中的折断风险。从刀具的试切综合能效比来看,在车铣复合机床结合机械振动钻孔技术加工该零件的油管孔,效率比在专用机床上提高7.5倍以上(纯切削时间),如图11所示。在车铣复合机床上加工还节省了来回更换夹具等造成的停滞时间,加工效率大幅度提升。
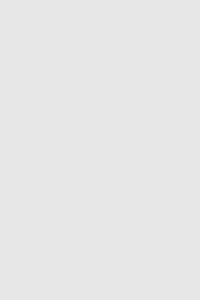 图11 车铣复合机床机械振动钻孔与传统专用机床钻孔加工时间对比 在金属切削加工过程中,孔加工的金属材料去除率约占金属切削加工总材料去除率的1/3,国内外先进的孔加工刀具、加工工艺及加工方法都在提升着孔加工效率及质量,但稳定、高效地加工微小孔、深孔依旧是我们面临的加工难题。
基于现场生产过程中碰到的孔加工难题,不仅需要在加工刀具上多借鉴、引用新型刀具,还需结合已有的孔加工理论知识,从加工工艺、加工方法上去验证,如机械振动钻孔加工技术、超声振动钻孔技术等新型的加工方法,都是解决深孔加工难题
的新措施、新手段。这些新的加工技术还要结合现场的机床、刀具、工件、工件材料及工件的装夹刚性、机床的冷却方式等因素,多验证、多实践,收集加工数据,积累经验,为我们制造能力的提升打下牢靠的基础。
参考文献: [1] 程军,焦锋. 微小孔钻削工艺的研究现状[J]. 机械工
程师,2007(11):9-11. [2] 何定健,李建勋,王勇. 深孔加工关键技术及发展[J]. 航空制造技术,2008(21):90-93. [3] 王峻. 现代深孔加工技术[M]. 哈尔滨:哈尔滨工业大学出版社,2005. [4] 米曾榜. 小孔加工[M]. 北京:机械工业出版社,2001. [5] 王世清. 深孔加工技术[M]. 西安:西北工业大学出版社,2003. [6] 马利杰. 轴向振动钻削机理及其工艺效果实验研究[D]. 镇江:江苏大学,2007. [7] 何朝晖. 微小孔旋转超声轴向振动钻削技术研究[D].
成都:四川大学,2004. [8] 韩旭. 深孔加工低频振动钻削试验研究[D]. 太原:中北大学,2007. [9] 艾冬梅,贾志新. 小孔加工技术发展现状[J]. 机械工程师,2000(1):8-10. [10] 吴东昇,陈学永. 振动钻削技术研究进展[J]. 机电技术,2014,4(2):150-153. 本文发表于《金属加工(冷加工)》2025年第3期15~20页,作者:庆安集团有限公司 陈栓,翟冲,孟凡华,原标题:《机械振动钻孔技术在大长径比深孔加工中的应用》。-End-
☞来源:金属加工 ☞责任编辑:徐裴裴 ☞校对:高晨旭 ☞审核人:吴晓兰
|