

一、基本统计概述 统计方法的意义 群体与样本 资料的分类 资料的分析 质量管制与统计方法


(一)统计方法的意义 
(二)群体与样本 样本〈Sample〉,为自群体中选取的一部分制品或半成品之测定值,或自整个检验批中抽取一部分制品或半成品之测定值。 样本〈Sample〉 ---> 以 n 表示。 计数值---> 样本不合格率 计量值 ---> 样本平均数 X ,样本标准差 σ x 样本的取得,特别应注意 随机性:并能够代表群体为原则。
(三)资料的分类 (四)资料的分析 (五)质量管制与统计方法 质量管制的发展阶段:操作员品管、领班品管、统计品管〈SPC〉、全面品管〈TQC〉、全面质量管理〈TQM〉,六大阶段。 自第四阶段的统计品管〈SPC〉,Dr. Shewhart 博士( 1924 年) 发表『制造产品质量的经济管制』以后,统计方法即持续运用于质量管制中。 举凡 (1) 市场分析 (2) 产品设计 (3) 可靠度规格,寿命 / 耐用性预测 (4) 制程管制 / 制程能力分析 (5) 质量水平 / 抽样检验计划之决定 (6) 数据分析 / 性能评估 / 缺点分析 等,均导入适当之统计方法。 可用之特殊统计方法及应用包含〈但并不限于〉:
(1) 实验计划法 / 因子分析 (2) 变异数分析 / 回归分析 (3) 安全性评估 / 风险分析 (4) 显著性检定 (5) 管制图 (6) 抽样检验 二、直方图 (一)直方图的意义 将测量所得的 Data 如时间、长度、硬度等计量值,划分成数个组间,计算各组间数据出现的次数,以便了解其分配的状况的图表,叫作直方图。 
(1) 测知制程能力 (2) 计算产品不良率 (3) 调查是否混入二个以上不同的 群体 (4) 测知有无假数据 (5) 测知分布型态 (二)直方图的应用 



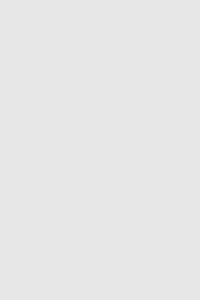
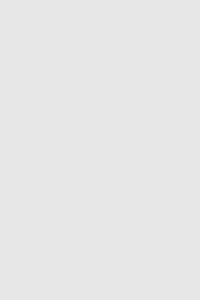
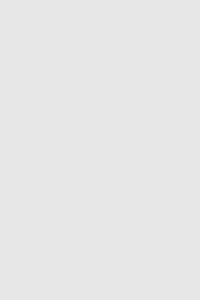
(例)有一机械厂,为了解制品外径尺寸之变化,由产品抽取100个样本测定其外径,测定结果如下表,试作次数分配表。 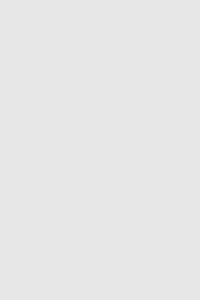
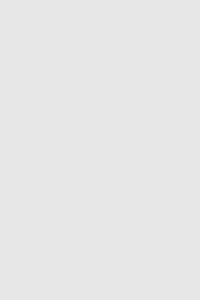
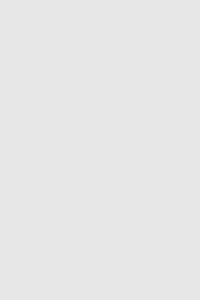
(三)次数分配表 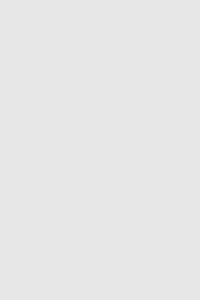
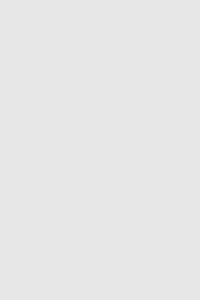
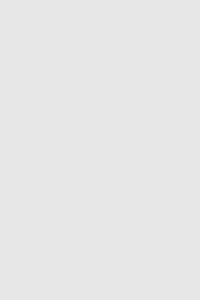
三、基本统计量数 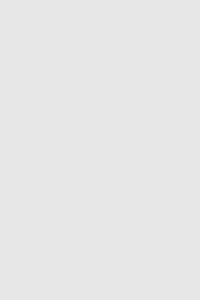
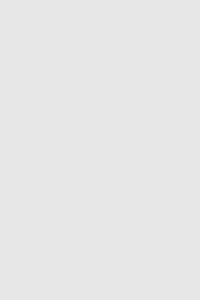
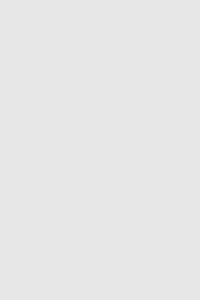
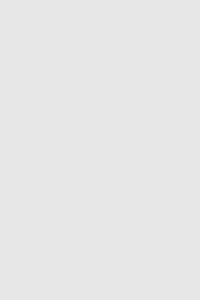
正态分布 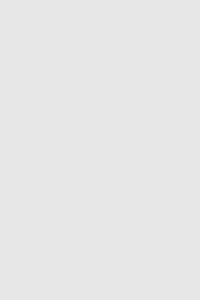
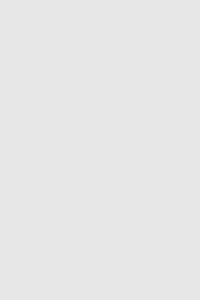
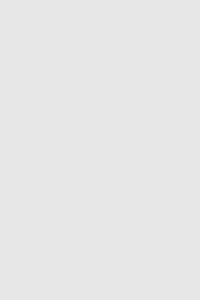
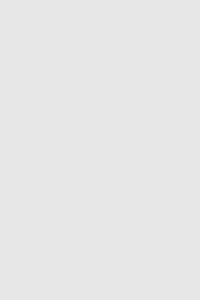
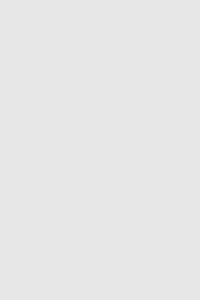
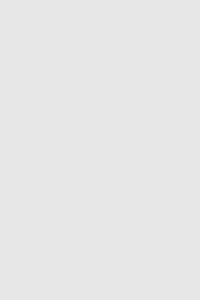
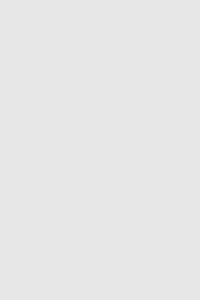
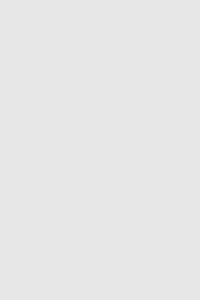
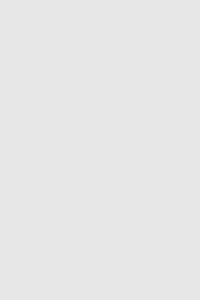
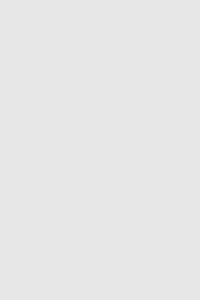
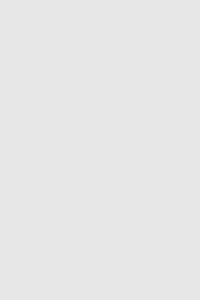
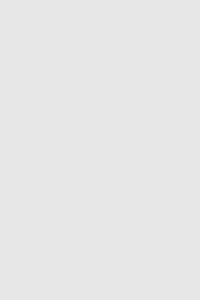
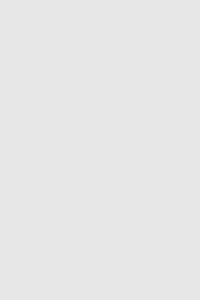
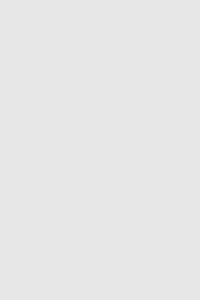
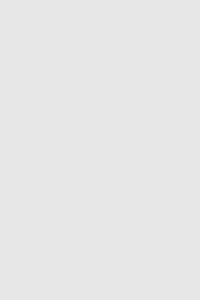
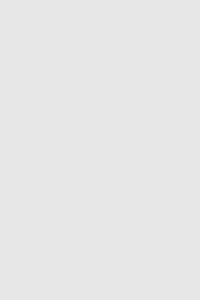
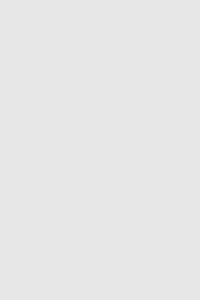
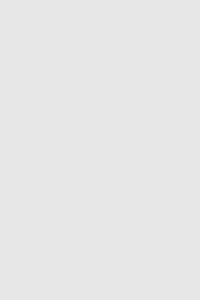
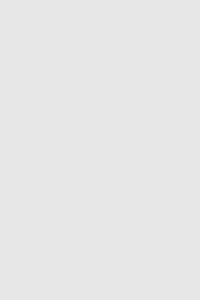
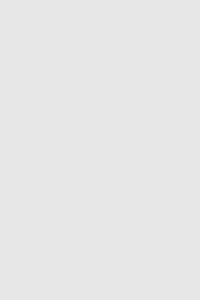
四、SPC背景说明 SPC 兴起的背景 SPC 的迷思 SPC 的焦点 SPC 的思考 SPC 的诊断
1. 对质量常有的错误观念 大多数的质量问题是错在作业人员 容许少数的不良,意外的瑕疵是无可避免的 质量是品管部门的责任 只重视质量检验,检验人员需负责解决瑕疵品 SPC只是在现场挂管制图
2. 对质量的正确观念 85%的质量问题是管理人员所要担负的,管理者态度的偏差,更胜过作业人员的懒散 第一次就把事情做好,并且将后工程视为顾客,才能真正做到零缺点质量 质量和公司每一个人都有关 质量检验是可以解决问题但却无法消除问题 SPC是让质量保证的系统持续运转不断改善制程,以提升质量与生产力
3. SPC 兴起的背景 SPC 兴起是宣告『经验挂帅时代』的结束 ─ 手工艺的产业:SPC 无用武之地→经验取胜 ─ 当经验可以整理,再加上设备、制程或系统时,那 SPC 时机的导入,就自然成熟了。 SPC 兴起是宣告『质量公共认证时代』的来临 ─ 1980年以前,客户大都以自己的资源与方法,来认定某些合格的供应商,造成买卖双方的浪费。 ─ 1980年以后,『GMP』及『ISO 9000』的兴起,因为重视产品生产的『制程』与『系统』,故更须有赖 SPC 来监控『制程』与『系统』的一致性。
4. SPC 的迷思 ─ 这是产品质量 ( Q ),还是制程参数 ( P ) 管制图? ─ 这张管制图是否有意义? ─ 它所管制的参数,真的对产品质量有举足轻重的影响吗? ─ 管制界限订的有意义吗? ─ 这张管制图,是否受到应有的重视?是否已遵照规定,实 施追踪与研判? ─ Cpk / Ppk 有定期审查吗? ─ 是否已用 Cpk / Ppk 作订单分派给不同生产线,作为生产 的依据 ? ─ 为什么挑出这些制程参数? ─ 这些制程参数的控制条件,是如何决定的? ─ 这些制程参数与产品质量之间,有因果关系可循吗? 5. SPC 的焦点 → 制程 ( Process ) SPC 与传统 SQC 的最大不同点,就是由 Q → P 的转变 SQC:强调 Quality → 产品的质量,换言之,它是着重于买卖双方可共同评断、鉴定的一种『既成事实』。 SPC:则是希望将努力的方向更进一步的放在质量的源头 → 制程 ( Process )上。因为制程的起伏变化,才是造成质量变异 ( Variation ) 的主要根源。 质量变异的大小,也才是决定产品优劣的关键
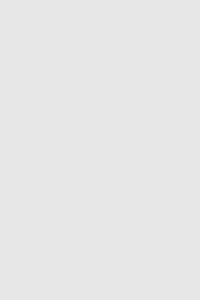
6. SPC 的思考 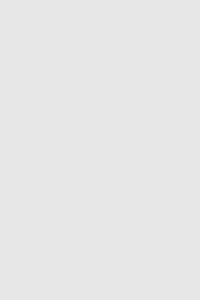
制程参数 (因) / 质量贡献率 (果) 分析 → 柏拉图分析 → 以回归分析方法或实验设计来分析 ‧控制频率 ‧样本抽取方法 ‧样本量测方法 7. SPC 的诊断 质量是否更稳定? 良品率是否提高? 制程是否更流畅? 成本是否更低廉? 异常是否更快能被侦测到? 品管员是否逐渐在减少?
五、制程变异 统计制程管制的定义 非机遇原因变异 机遇原因变异 制程控制与制程能力 制程改善循环
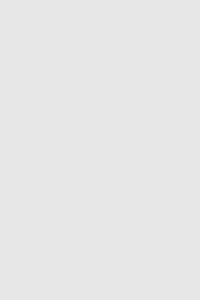
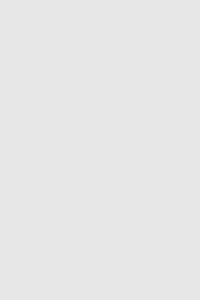
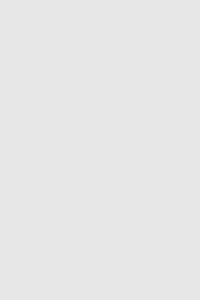
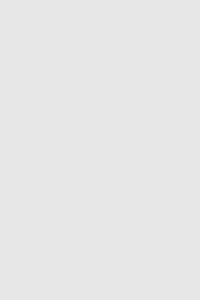
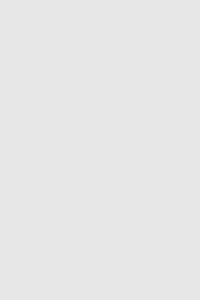
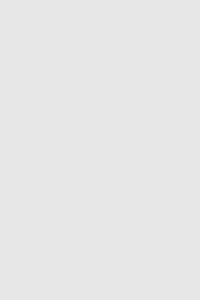
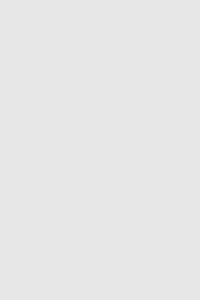
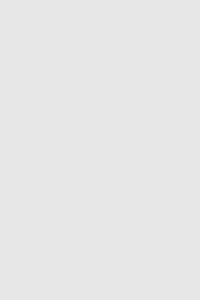
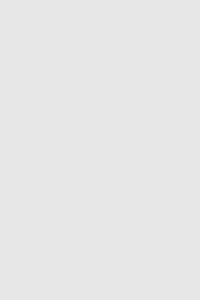
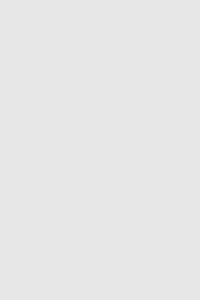
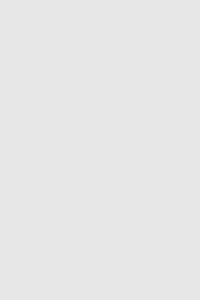
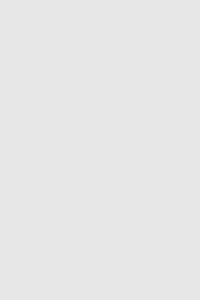
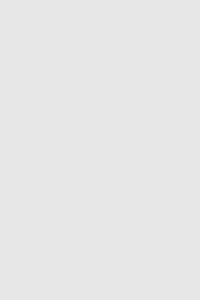
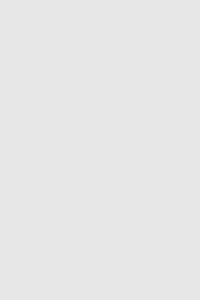
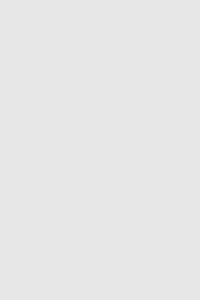
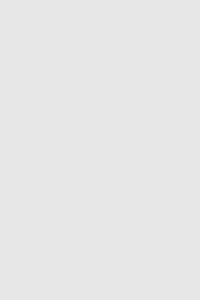
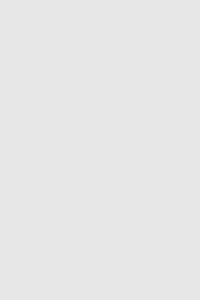
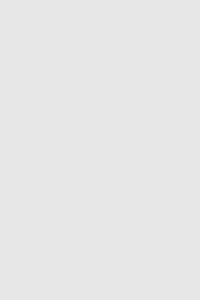
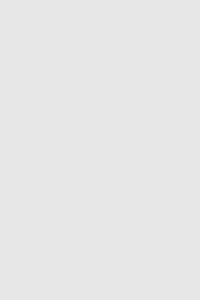
六、建立 SPC 的步骤 确立制造流程、制造流程解析 决定管制项目 实施标准化 管制图的运用 制程能力分析 问题分析解决 制程的继续管制
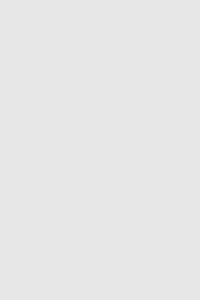
流程定义 藉由所需的人员、程序、机器、物料等(输入) ,经由必要的作业活动来产生一特定的产品或 信息 (输出) 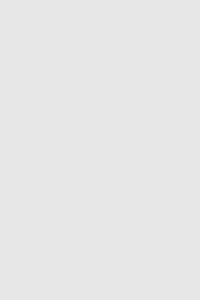
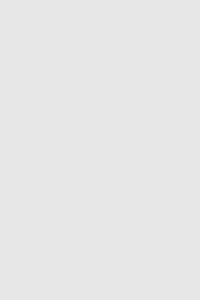
决定管制项目
为维持产品的质量,作为管制对象所列举的项目 → 特殊特性: 尺寸、材质、性能、外观 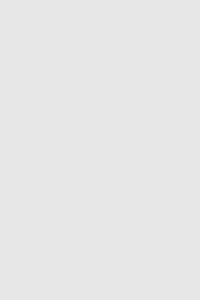
3. 实施标准化 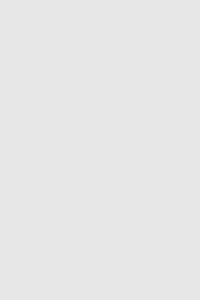
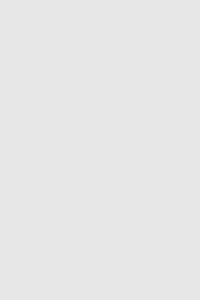
4. 管制图的运用 管制图是1924年由萧华特博士(Dr.W.A.Shewhart),在研究产品质量特性之次数分配时所发现。正常工程所产生出来产品之质量特性,其分布大都呈正态分布的,会超出三个标准差(3)的产品只有0.27%,依据此原理,将正态曲线图旋转90度,在三个标准差的地方加上两条界限,并将抽样的顺序点绘成为管制图。 1) 使用管制图的效益 2) 管制图的种类 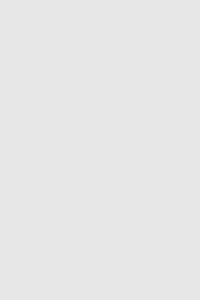
3) 管制图之管制上 / 下限 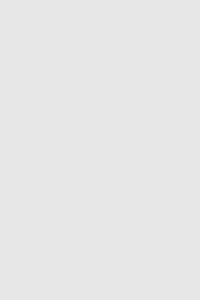
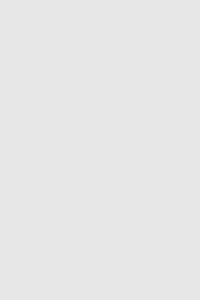
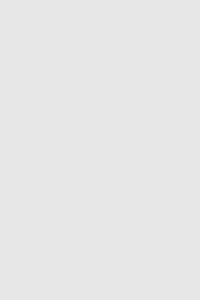
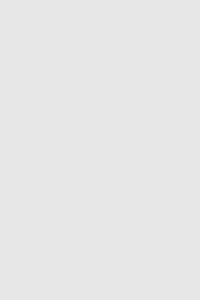
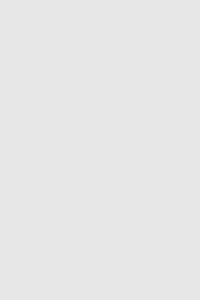
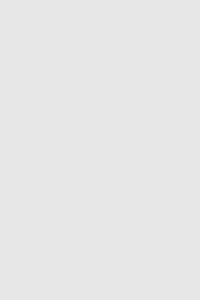
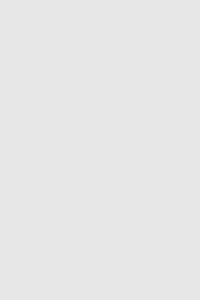
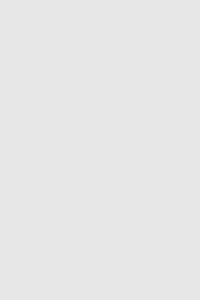
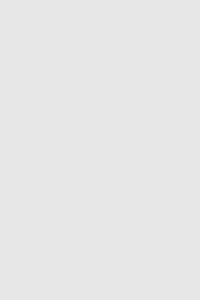
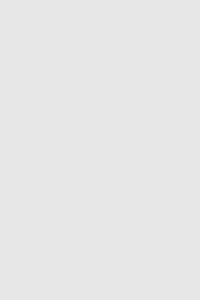
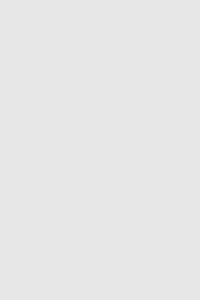
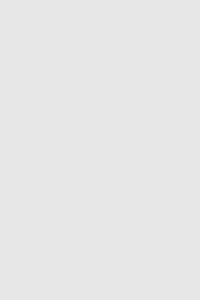
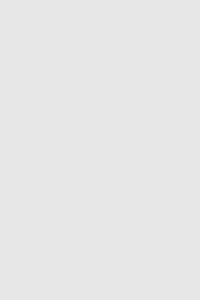
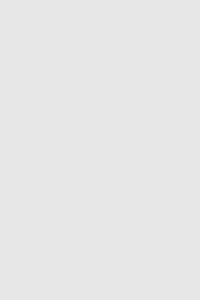
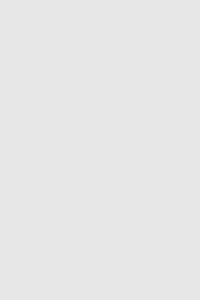
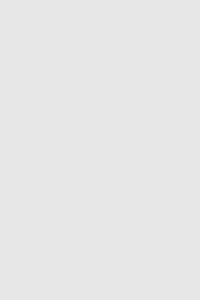
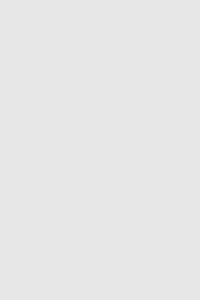
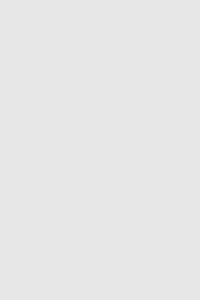
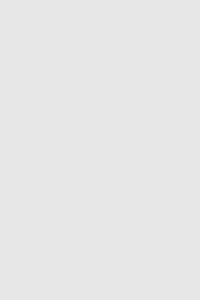
5. 制程能力分析 制程处于『受控』状态 制程的各测量值符合『正态分布』 工程及其他规范准确的代表顾客的需求 设计目标值位于『规格的中心』 测量变异相对较小
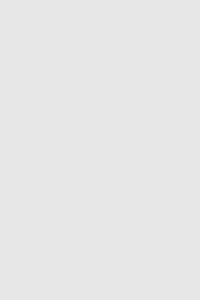
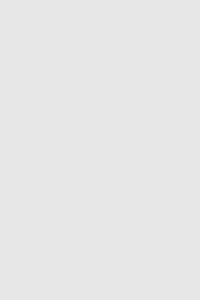
1) 制程能力调查步骤 确切了解要调查的质量特性与调查范围,并收集数据 制作解析用管制图,确定制程处于受控状态之中 计算制程能力指数 ( Short Term : Cpk ) 判断制程能力是否足够,如不够时或不稳定时,则加以改善 以解析用管制图之『管制上、下限』,作为『管制用管制图』之监控,并于一段期间后,再计算制程能力指数 ( Long Term : Ppk )
2) 制程能力调查的方式 3) 图示法制程能力的初步判定 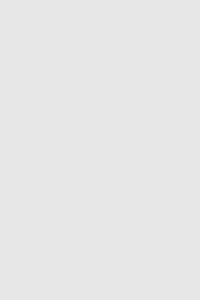
4) 数值法制程能力分析 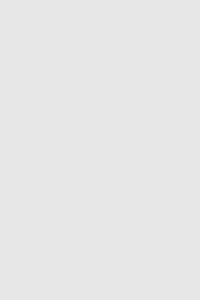
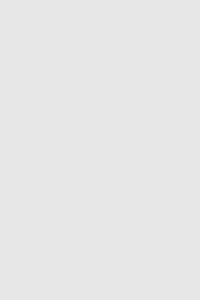
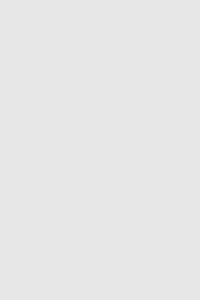
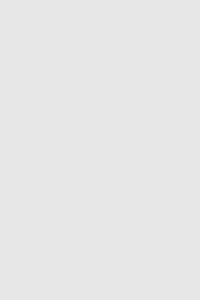
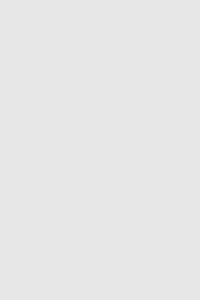
5) 制程能力指数 Cpk( 稳定的制程 ) 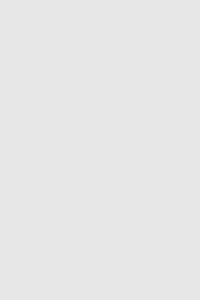
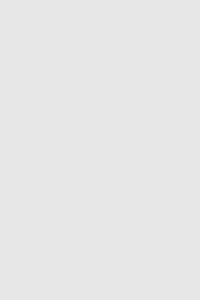
6) 制程能力指数 Cpk ─ S.T. Stable Process 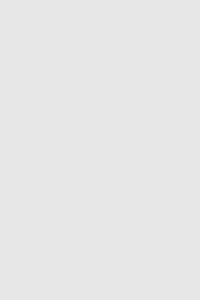
7) 性能指数 Ppk ─ L.T. 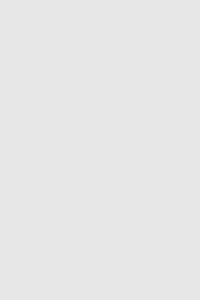
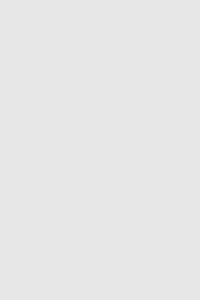
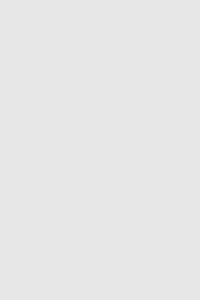
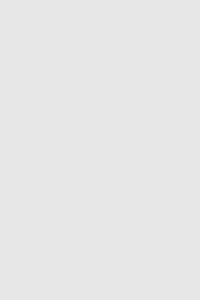
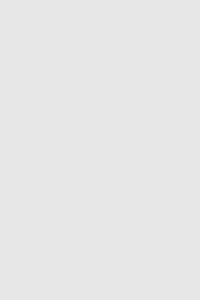
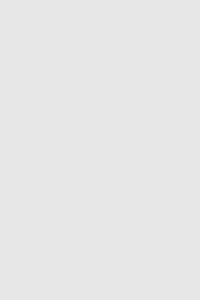
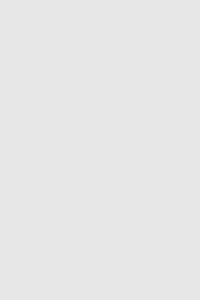
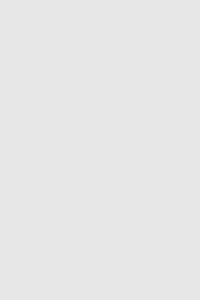
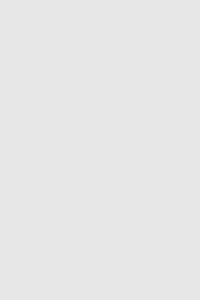
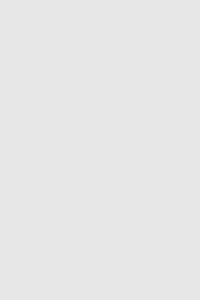
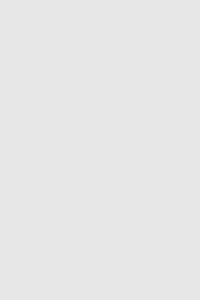
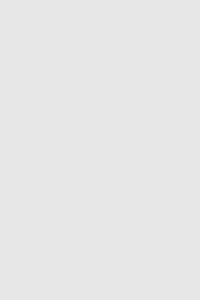
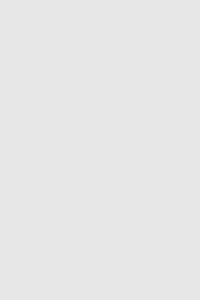
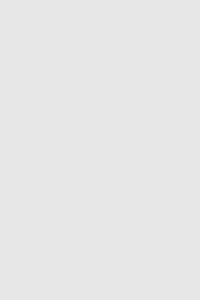
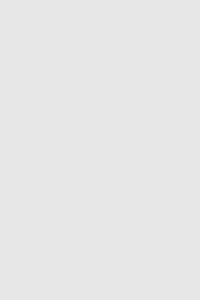
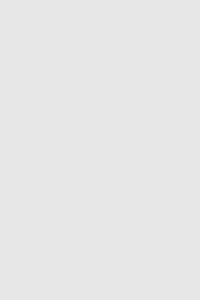
|